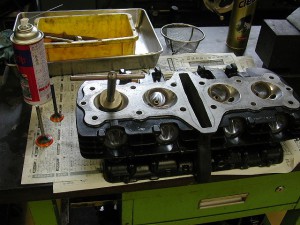
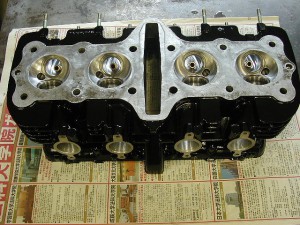
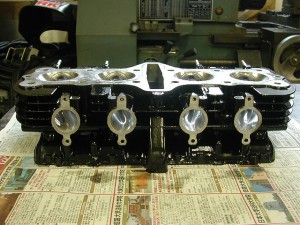
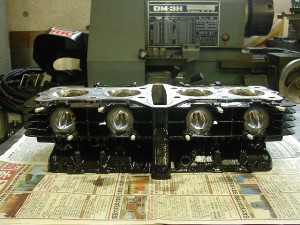
リーマー通しが終わったら、バルブシートカッターでバルブシートを成型します。
成型と同時にバルブが垂直にシートに収まるように
シートとガイドとの傾きを修正します。
この時、ガイドとバルブステムにはクリアランスがあるので、
その範囲なら何処でも垂直が出てしまうのですが、
なるべくクリアランスの中心で芯−芯が出るように慎重にシートカットします。
シートカットが終わったらバルブのすり合わせを行います。
バルブのすり合わせ時の音と手ごたえでバルブの密着度を判断します。
これは長年やっているとかなり正確に状態がわかるようになります(笑)
なので確認の為の光明丹は使いません。
余談ですが、このあたりの加工はかなりシビアなので、
量産車の新品ヘッドを分解すると
加工の僅かなズレや刃物のビビリなどでバルブがうまく
密着していない物もあります。
アタリが出ていなければ当然ガスの噴き抜けなどを起こして
性能が低下してしまいます。
エンジンの当りハズレなどはこんなところも影響していると言う事でしょう。
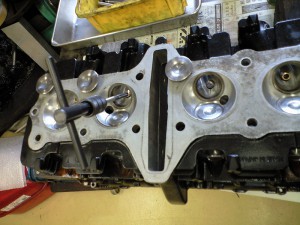
バルブガイドを打ち変えたらリーマー通しという作業で
新品ガイドの内面を削ります。
なぜ削る必要があるかと言うと、ヘッドに打ち込まれた
バルブガイドはきつく締め付けられて、内径が小さくなってしまうからです。
そこで穴寸法を出せるリーマーという工具を使って削ります。
しかし、刃に掛かる圧力が高い(内径が小さい)時は問題無いのですが、
ある程度からは刃が逃げ始めて削れなくなってくる場合があります。
その状態でもバルブは問題なく通るのですが、クリアランス不足で
あとからバルブステムの焼き付きのトラブルが起こる事があります。
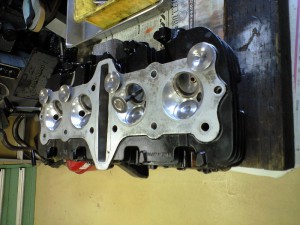
これは古いバルブでガイドをラッピングしているところです。
ラッピングしながらリーマーを通し、同じ抵抗で通り抜ける
ようになるまで繰り返します。
こうすることでリーマーがゲージ代わりになって正確な穴寸法が得られ、、
クリアランス不足の焼き付きを防ぐ事が出来ます。
そして以上の作業を、なるべくバルブシートとの
直角が出るように力を加減しながら進めます。
手作業で手間が掛かりますが、バルブシートの修正が最小限で済み、
圧縮圧力の低下やバラつきを抑える事ができます。
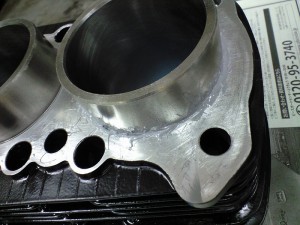
例のスリーブが圧入&ボーリングされて帰ってきました。
かなり分厚いです(笑)
スリーブとシリンダーブロックのスキマをコーキングします。
オリジナルだとここにはオーリングが入るんですが、
効果を発揮する寿命が短いので、シリコンで溝を埋めます。
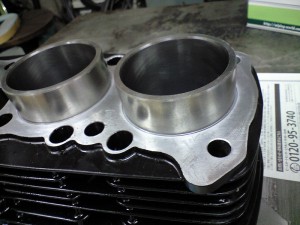
ハミでた分を落として綺麗に仕上げました。結構手間かかります(笑)
通常ならこんなに手間をかけなくても大丈夫ですが、
今回はシリンダーブロックをボーリングしているのでこの方法です。
シリンダースリーブと違い、シリンダーブロックはそもそも
ボーリングを想定して作られていません。
なので、ボーリングすると予想外の事が起こる場合があります。
内側の切削面に、それまで隠れていた鋳造時のス(小さい穴)が現れて、
内側と外側を繋げてしまい、変な所からのオイル漏れの原因になったりします。
組んだ後ではうまく対処しずらいので、事前にココを封鎖しておくのです。